实现虚拟化智能工厂,通过物联网、互联网、大数据、人工智能、数据通讯、三维建模、虚拟现实等技术,实现物理实体工厂和孪生虚拟工厂双向实时映射。物理工厂设备的运行状态与孪生工厂实时同步。
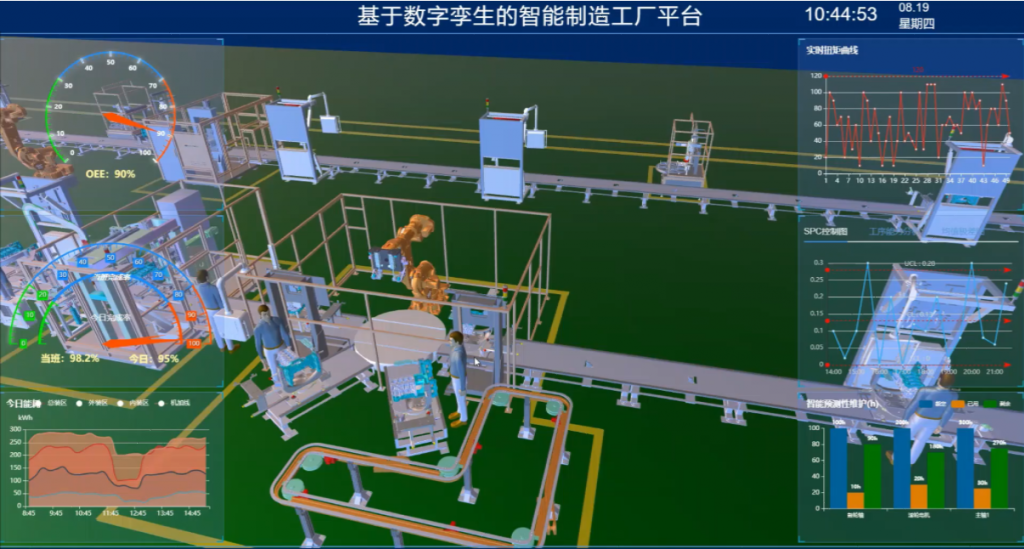
实现对机加工车间、装配车间的生产管控智能化升级,包括:生产计划下达、智能排产、工艺防错、报工、设备管理、物料管理、质量追溯、AGV自动化物流等生产过程实时监管,通过办公室大屏幕看板可以远程实时了解生产现场状况,订单执行情况、设备运行状态等,可通过直观的数据图统计分析,实现生产管理数据透明,有针对性突破管理瓶颈。
应用数字孪生技术,实现工艺设计环节的仿真优化、虚拟调试;实现生产作业环节的关键设备实时运行数字孪生可视化;实现设备管理环节的设备刀具、主轴等关键部件预防性维护、寿命管理。
(一)工艺设计环节
- 应用CAPP软件进行产品工艺设计,应用数字孪生技术在产品设计环节,工艺仿真、虚拟调试。
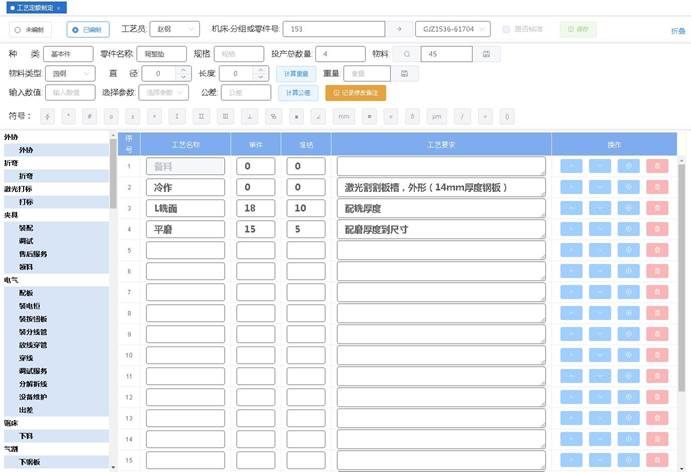
工艺设计
应用数字孪生技术,实现了数字化三维设计与工艺设计,让机械工程师可以在设计初期,通过设备的虚拟孪生模型对产品的设计进行仿真验证,干涉检验,及早发现设计缺陷。通过虚拟样机实验实现闭环的设计优化,改变传统串行设计流程,实现并行的机电一体数字化设计模式。
1)应用数字孪生的运动仿真进行干涉验证,在早期发现设计缺陷,减少后续的返工损失。
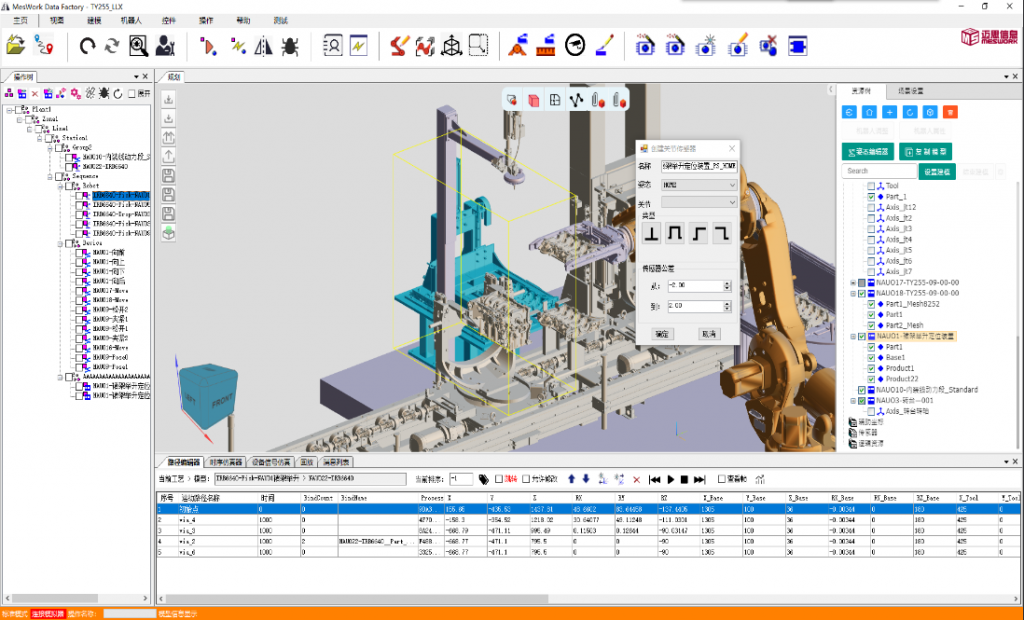
设备工艺仿真参数化定义界面
2)可进行工艺时序仿真,验证和优化节拍及工艺参数,提高工艺设计水平。
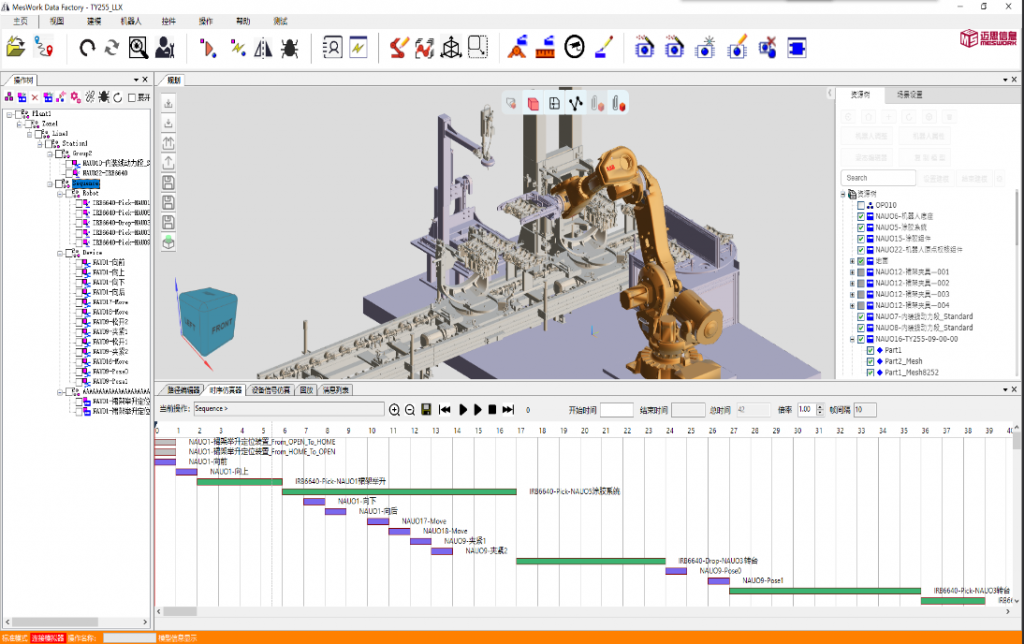
工序仿真
(3)生产线或机床数控程序可在虚拟样机下离线编程优化,减少对实体设备的依赖,减少停机实验造成的成本,减少新工艺准备周期。
- 通过建立产品数据管理系统(PLM),实现研发项目管理,产品设计、工艺数据的集成管理,有效组织生产工艺过程卡片、零件蓝图、三维数模等生产作业文档。
(1)利用CAPP进行工艺设计与编制,并将典型工艺存于数据库中直接拷贝调用,实现工艺BOM管理。
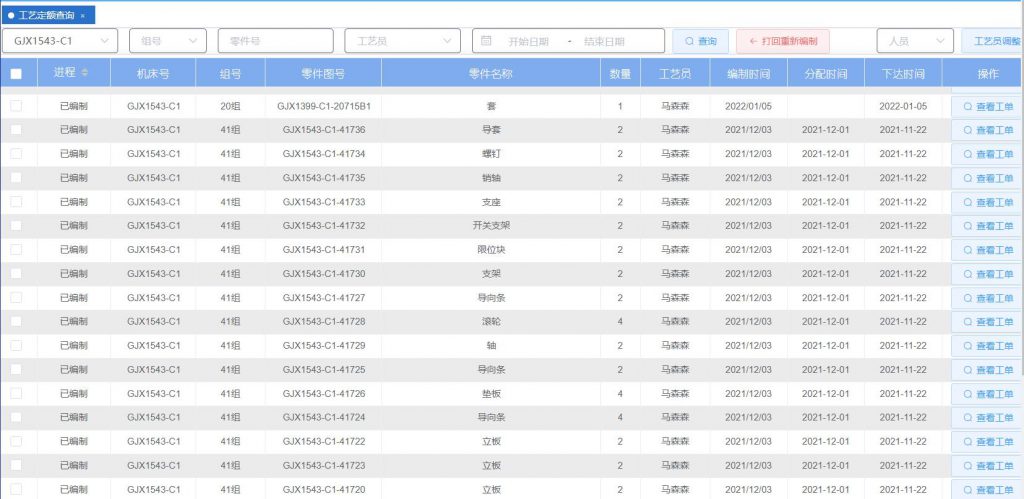
工艺数据管理
2)对产品设计数据统一管理,并建立研发设计案例库,将产品的设计图纸导入库中进行在线的分析、共享和管理。
(二)生产作业环节
1、建立MES系统,系统数据自动获取生产计划,并下达至加工中心具体工位,并根据工单内容附带工艺指导书及物料清单BOM,操作工可以通过现场工控机界面,查询工单任务,并根据作业指导书进行标准操作,在完成后报工。现场工位电脑配备扫码枪,可提供关键物料的扫码录入、防错。同时具备ANDON报警,生产管理人员可以通过大屏幕快速发现异常,调度处理。
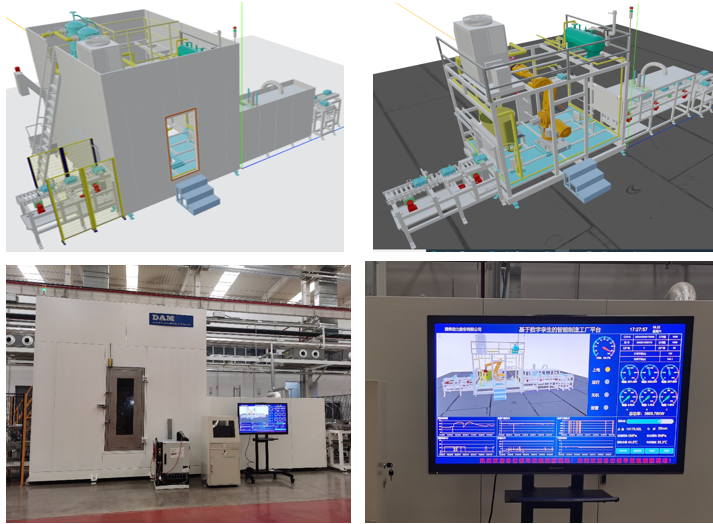
2、零件在生产过程中,通过条码扫描跟踪零件在线状态,监控零件流转过程,保证零件在车间生产过程中快速高效流转可追溯。
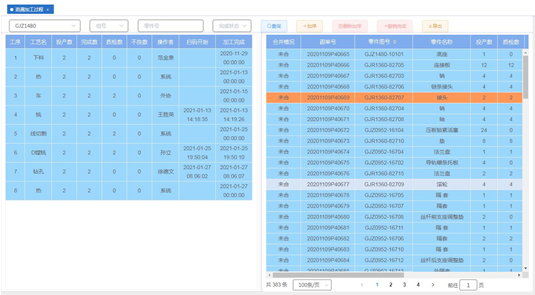
零件加工过程追溯
3、自动下发工艺文件至生产设备,通过数字孪生可视化应用,可以实现整个加工区域或单台设备实现运行过程的3D可视化显示,对关键工艺参数、设备运行数据等进行动态监测、自动采集和在线分析。
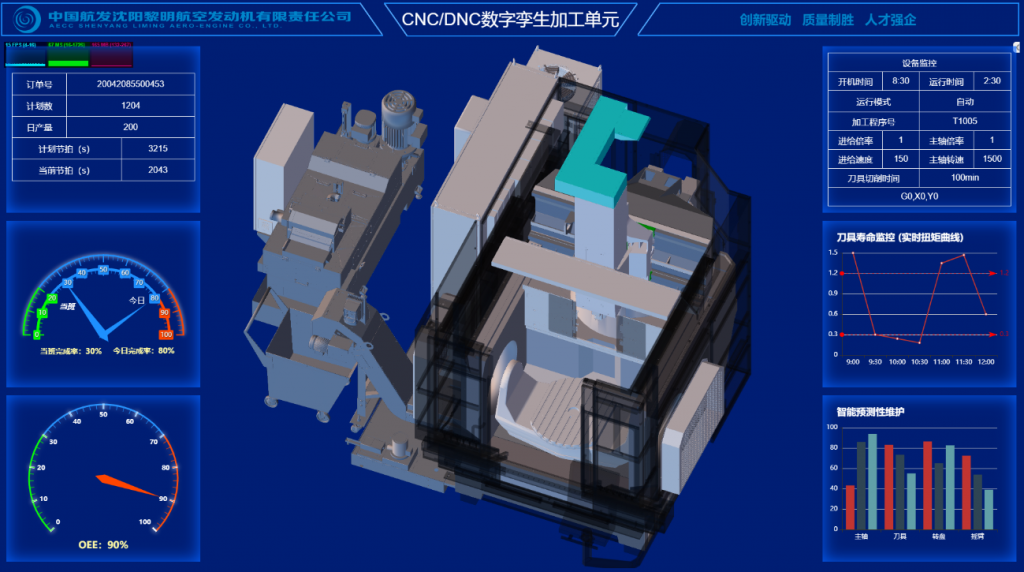
数字孪生设备监测
4、通过现场大屏幕或远程大屏幕可以实时查看生产现场情况。
(1)通过大屏幕可以远程查看数字孪生产线及设备的整体运行情况,3D孪生模型可以旋转、放大、缩小,并从各个角度浏览查看,可显示当前生产订单完成情况、产品合格率、综合OEE等生产数据;
(2)通过采集数控设备的伺服值,可以获取加工轴实时的位置,真实映射设备当前的加工轨迹;
(3)点击具体设备,可以查看其详细信息及关键运行参数;
(4)可视化界面可以显示设备编号、运行状态,以及主轴速率、倍率、刀具使用时长等关键运行数据。通过报警信息,可以快速锁定设备,便于现场人员的调度。
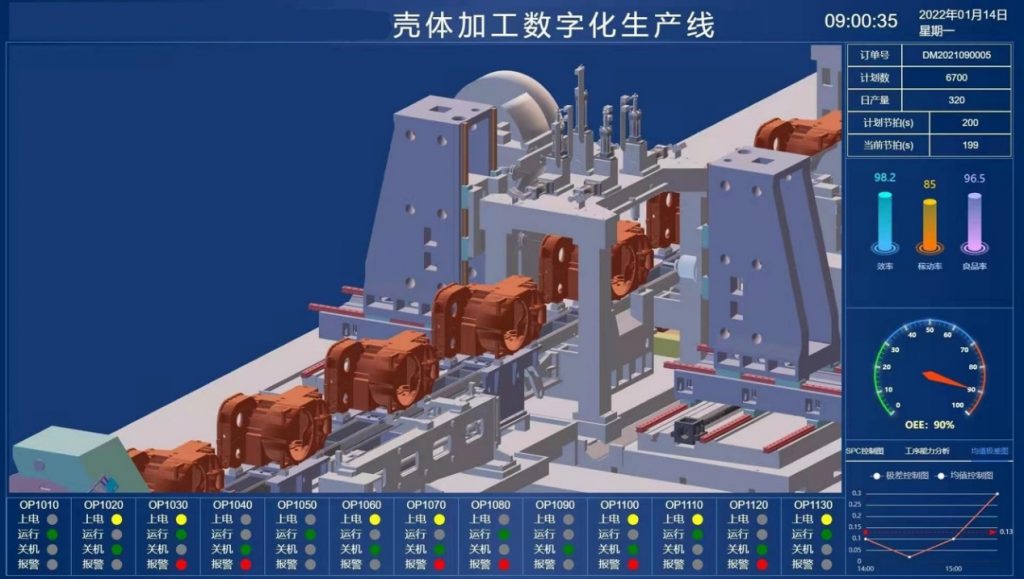
车间产线设备数字孪生可视化看板
(三)设备管理环节
智能工厂所有关键工序设备皆为自动化数控机床,且实现了设备的互联互通,运用智能感知与控制、机器视觉、边缘计算、数据可视化管理,实现设备资产管理、设备健康监测、设备生产状态实时监控等功能。
通过智能工厂的设备生产监控平台,可总览查看全厂设备运维状态。当光标悬停在某台设备上时,可以查看该设备正在加工的工件信息,单击某一工位,可以查看该设备详细状态和生产信息。
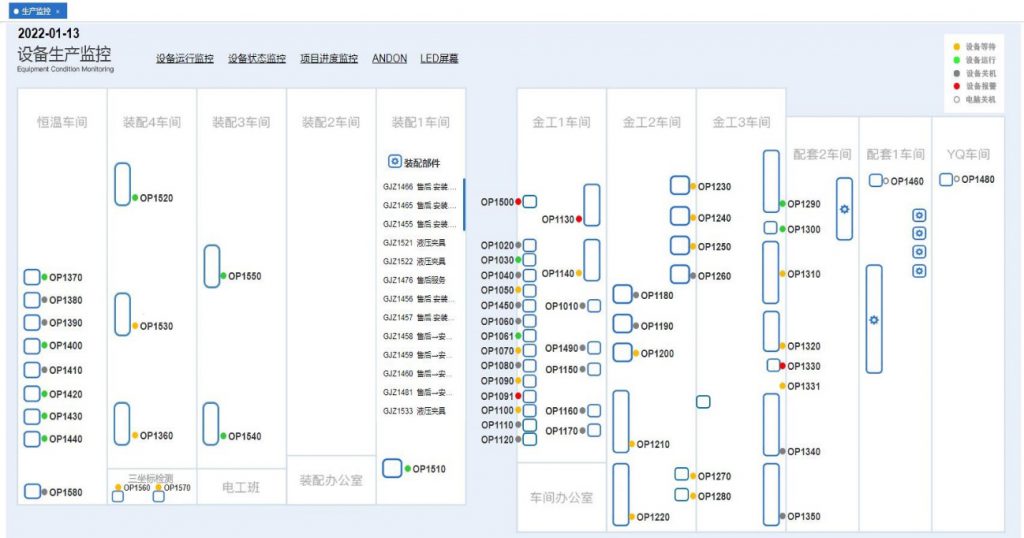
设备实时监控
通过对平台中产生的海量数据进行筛选、压缩,去除冗余和无效数据从而保证了数据的准确性、有效性和可靠性,同时结合需求设置相应的算法对处理后的数据进行分析从而得出相应的结论。如:通过对设备采集的数据进行处理得到设备的状态分布情况,再通过对状态分布的数据进行分析,得到设备的有效利用率,示例如图所示。
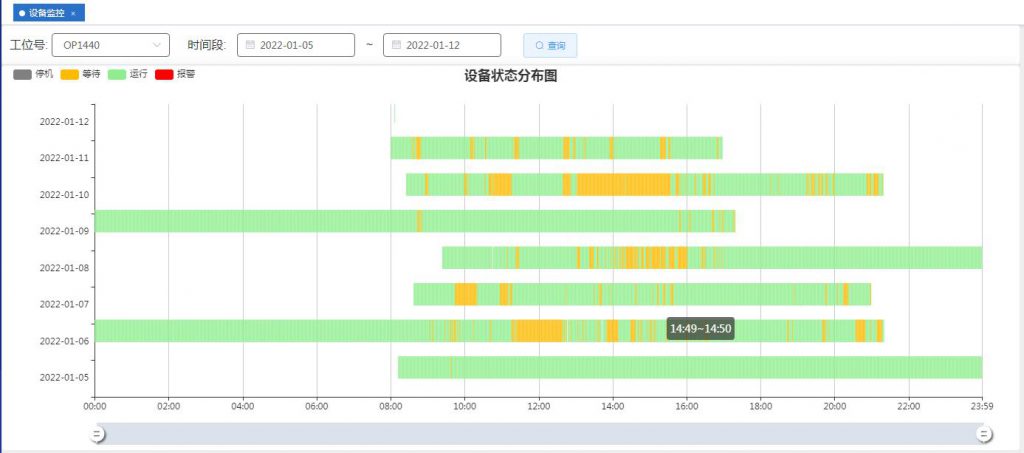
设备状态数据处理
通过智能工厂关键工序自动化设备数字孪生平台,可以实现工艺模拟、加工程序仿真等功能。创建设备的三维模型,将设备加工的工艺属性附加到三维模型中,采用虚拟PLC控制模型进行工艺调试和仿真,最终交付产品的虚拟数字样机。在调试阶段,数字样机接收现场PLC控制,对数字样机进行虚拟设计,并将虚拟调试结果应用于现场。实现产品的可制造预测与设计、工程与工艺一体化仿真优化。
设备台账、点检、保养、维修等管理实现数字化。通过设备通讯接口或外部传感器采集设备运行参数,自动在线监测设备工作状态,实现设备故障自动报警,以及刀具等关键部件的寿命预测。
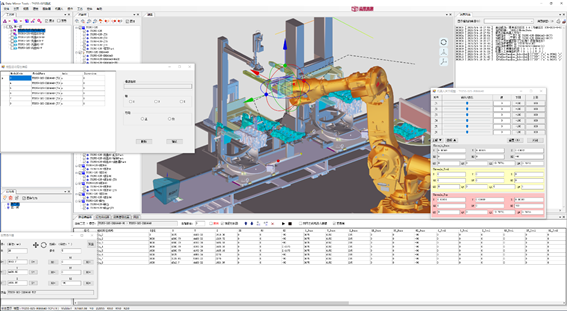
基于数字孪生平台还可以监测主轴等关键部件的扭矩、电流等重要参数,进行设备使用报警。通过建立预防性维护及设备寿命管理,改变传统的周期性、被动式设备维保模式,降低异常停机对生产的影响,提高设备OEE(设备综合稼动率),最终提高订单交付准时率。
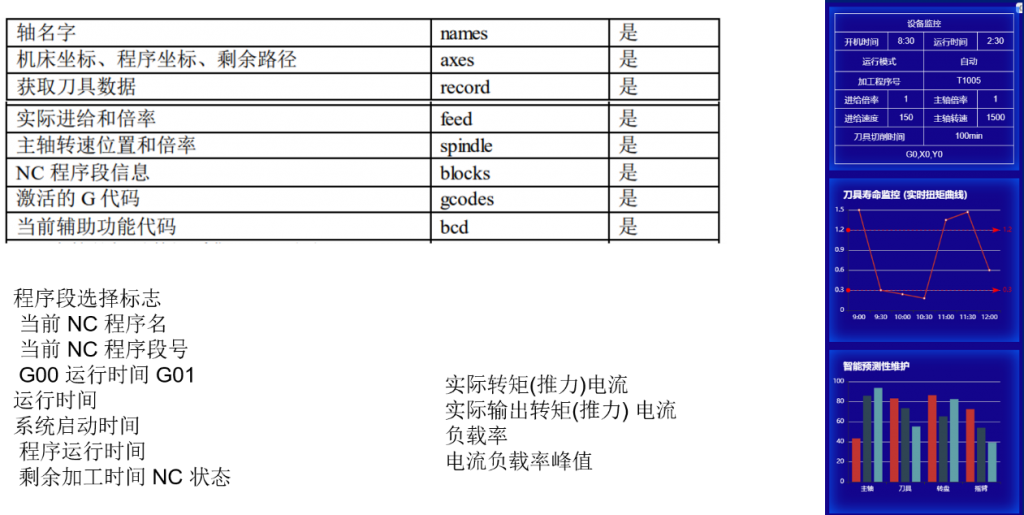